Unlocking the Power of Condition Monitoring: Key Benefits You Need to Know
A condition monitoring system is a game-changer for organizations looking to streamline their maintenance processes. This system offers benefits that can improve the performance and productivity of the machines used in an industry. The machine condition monitoring system market is making marvelous breakthroughs by developing efficient and more powerful systems.

Maintenance doesn't always have to mean costly repairs, but unfortunately, many organizations tend to think in that direction. The traditional approach often involves using assets until they break down, leading to unexpected expenses and downtime. However, there's a smarter way to handle maintenance, and it's called a condition monitoring system.
What Is a Condition Monitoring System?
A condition monitoring system is a game-changer for organizations looking to streamline their maintenance processes. It's all about automating asset health tracking to minimize the risk of sudden failures. Instead of waiting for breakdowns, this system employs predictive maintenance techniques, utilizing sensor data collected in real-time to gauge machine health and safety.
The benefit of a condition monitoring system is that it can notify you when an asset problem or performance issue is detected. This proactive approach to maintenance, which is similar to preventative maintenance, enables scheduled maintenance and prevents the occurrence of expensive breakdowns. The global machine condition monitoring system market is expected to boom with a CAGR of growth rate of 7.9% from 2023 to 2032, according to Research Dive. Now, let's dive into the advantages this system can bring to enhance your machine performance and productivity:
Advantages of a Condition Monitoring System
Monitoring Assets in Real Time
With a condition monitoring system, you gain real-time insights into your machines’ health. Maintenance is triggered only when certain indicators deviate from expected values, such as vibration, temperature, and key performance indicators (KPIs).
This constant supply of data can be an absolute treasure for assessing KPIs, improving productivity, and making thoughtful decisions about equipment performance, purchases, and supplier contract renewals.
Minimized Maintenance Expenses
Unexpected asset failures can be extremely costly. Real-time asset monitoring enables substantial cost savings by allowing you to proactively address issues and avoid expensive emergency repairs. Owners must be aware of the condition of their assets to save maintenance costs.
Extending Asset Life
Preventing unexpected shutdowns safeguards an equipment's physical integrity, reducing the need for costly component replacements. When original parts remain in place, and assets are consistently maintained, their lifespan naturally extends. This, in turn, leads to lower operational costs.
Prioritizing Maintenance Activities
Regular updates on equipment and assets can help create a prioritized list of maintenance tasks. This not only facilitates communication with maintenance teams but also helps organize projects efficiently. This helps avoid production delays and time wastage by focusing on planned maintenance projects.
Reducing Downtime
Timely maintenance boosts asset performance and uptime. To minimize sudden equipment failures and downtime, it is crucial to stick to your maintenance schedules. For organizations with a large number of assets, investing in an automated maintenance system, such as a
condition monitoring system can be a game-changer.
The Expansion of Machine Condition Monitoring System Market
Machine condition monitoring system manufacturers are continually pushing the boundaries of innovation to expand the global market size. For instance, in June 2021, Rexnord, a worldwide frontrunner in motor, air handling, and power transmission solutions, made a significant stride by introducing the industry's first Universal Smart Condition Monitoring System. This groundbreaking system has the capability to monitor critical parameters such as oil quality, temperature, and vibration on a wide range of large gear drives. Such developments are revolutionizing the way industries monitor and maintain their machinery, offering more comprehensive insights and further enhancing the effectiveness of condition monitoring systems worldwide.
The machine condition monitoring system market is making marvelous breakthroughs by developing efficient and more powerful systems. Embracing this technology is a smart move for organizations looking to thrive in today's competitive industrial landscape. In a nutshell, organizations shouldn’t wait for breakdowns, instead they should take control of the maintenance processes by putting in place a condition monitoring system.
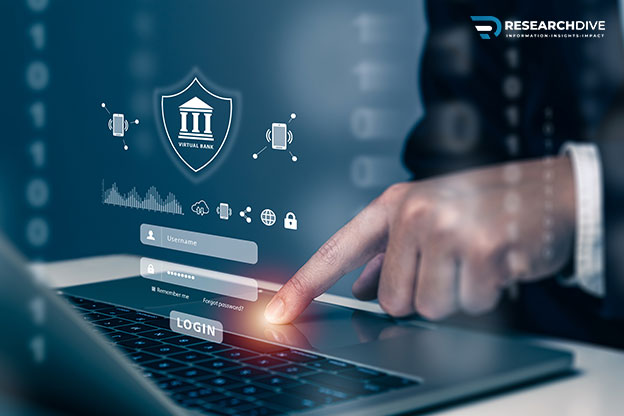
How is Cybersecurity Becoming a Vital Measure to Combat Emerging Threats in the Banking Sector Globally?
April 08, 2024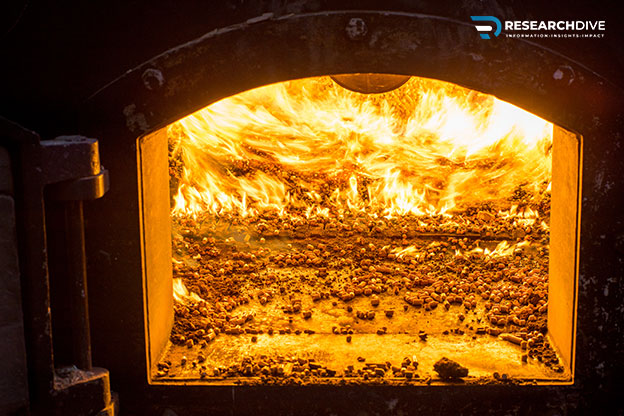
Wood Pellet Biomass Boilers: An Eco-Friendly Heating Solution
April 08, 2024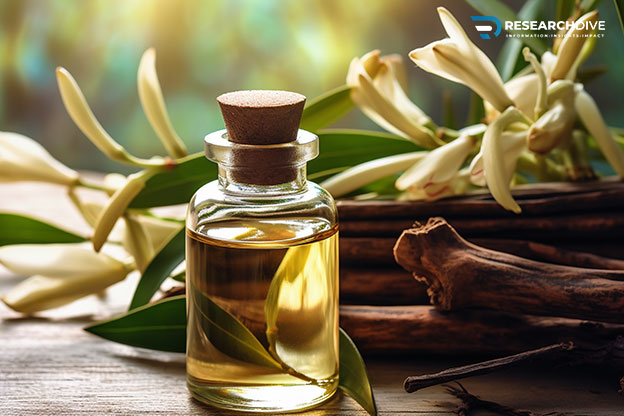
5 Ways Vanilla Oil Can Transform Your Life
April 08, 2024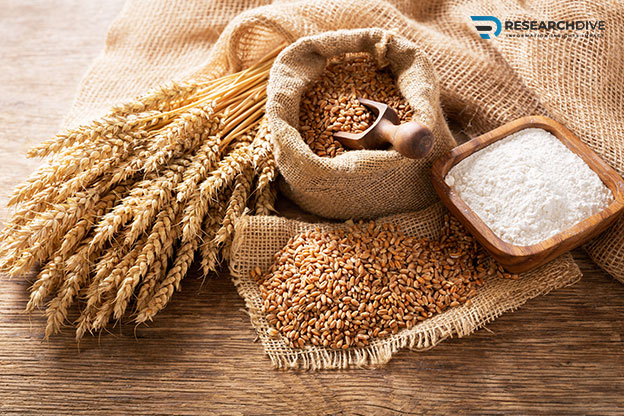
Discovering the Magic of Toasted Flour: Why & How to Use It
April 08, 2024