The Need for Oil Condition Monitoring in Today's Industrial World
Oil condition monitoring predictive maintenance programs assist clients in avoiding equipment failure by monitoring machinery lubricant quality. Machine operational problems are frequently reflected in the state of the lubricating oil used. Regular oil condition monitoring helps spot mechanical issues before they have an impact on how efficiently machinery operates.

Oil is typically used to run industrial units. Whether used as a fuel or lubricant, oil is usually responsible for preserving the effective operation of industrial processes. In order to diagnose faults, schedule maintenance based on data, and implement early warning systems, oil condition monitoring is useful.
What is Oil Condition Monitoring?
Oil condition monitoring (OCM) is an essential component of any predictive maintenance program. OCM includes monitoring, analyzing changes, measuring fuel oils and lubricants for chemical content and contamination, and tracking the deterioration in oil quality from new through end-of-life. The growing need for affordable solutions to keep machines in good condition is expected to boost the growth of the global oil condition monitoring market.
Why is it Necessary to Monitor the Oil Condition?
An accurate, high-quality oil condition evaluation gives a comprehensive understanding of the condition and health of your equipment. Oil that has been contaminated by fuel, water, or acid can lose its lubricating capabilities very fast, causing equipment damage in the process. As the state of the oil decreases with use, one can pinpoint the exact period for maintenance, thus extending service intervals.
What are Different Ways to Implement OCM?
- Oil Quality Sensors
Oil quality sensors enable non-chemists to undertake real-time oil condition monitoring. This eliminates the hassle of gathering samples and mailing them to professionals. Thus, the development of oil quality sensors has greatly simplified the OCM process.
- Testing and Analysis
One of the typical methods used by airlines to check the state of their engine oil is to send a sample to a lab for analysis. The engine is sampled either by pulling it out with a vacuum pump or by removing the oil drain plug and allowing enough oil to run out to fill the sample bottle. Then you email them or send them by delivery service, such as FedEx or UPS, to the lab of your choice. Inspection and testing are done there.
Some of the Effective Benefits of OCM
- Find Problems Before They Occur
Knowing in advance that the equipment may have a problem might save both time and money. OCM provides a comprehensive examination of a equipment's lubrication. Small faults can be found and fixed with regular oil testing before they grow into larger ones. OCM is used to identify specific wear patterns in particular equipment sections.
- Longer Lasting Equipment
Regular inspections and maintenance significantly extend the equipment's usable life and improve productivity across the board for the entire plant. Early detection with OCM is useful not only for avoiding high maintenance expenditures or lost productivity but may also improve the general working health of the machine and help the equipment survive longer.
- Fewer Repairs and Less Down Time
The majority of significant mechanical issues begin modestly and get worse over time. Larger issues may require substantial repairs and, as a result, significant downtime for a machinery and the entire factory unit. OCM allows an early detection of elevated wear metal levels that indicate an internal component breakdown. Cross or external contamination is indicated by particle counts, additive levels, and even increasing viscosity trends.
The Bottom Line
Regular OCM on your lubrication system can provide crucial information about how well an equipment is running. As lubrication is important to keep a factory machinery operating at peak efficiency, taking good care of the lube system and receiving timely alerts to take good care of the factory’s whole operational system is essential. To sum up, the key to preventing component failures and maintaining equipment in the best possible condition is establishing a regular OCM program.
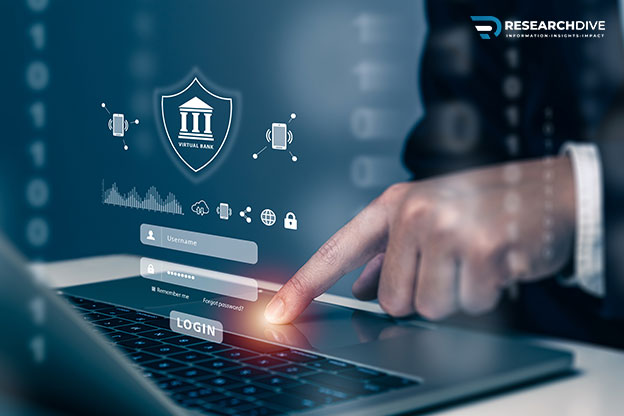
How is Cybersecurity Becoming a Vital Measure to Combat Emerging Threats in the Banking Sector Globally?
April 08, 2024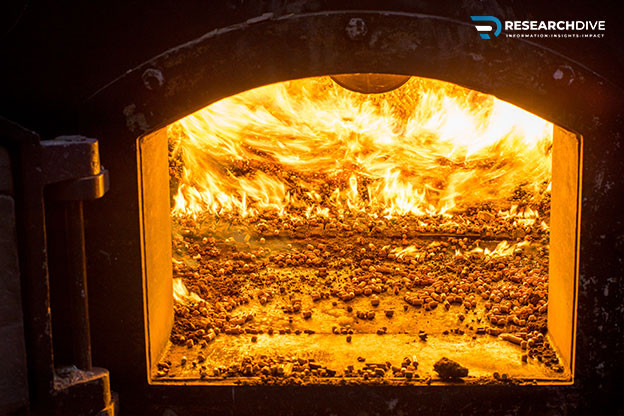
Wood Pellet Biomass Boilers: An Eco-Friendly Heating Solution
April 08, 2024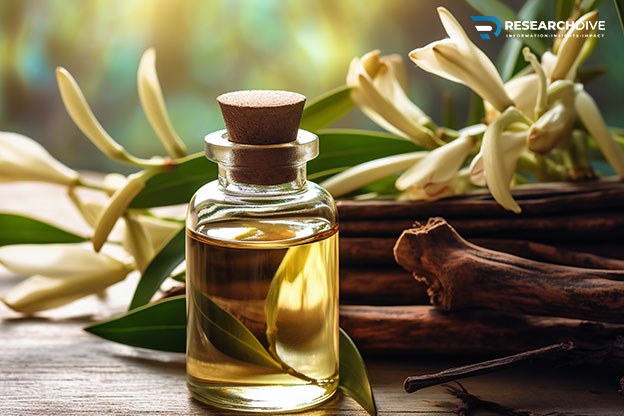
5 Ways Vanilla Oil Can Transform Your Life
April 08, 2024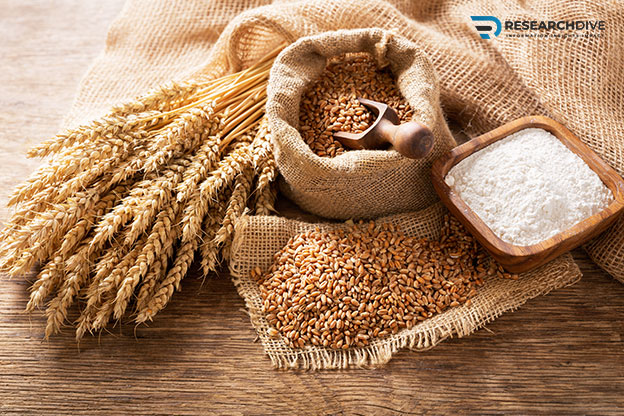
Discovering the Magic of Toasted Flour: Why & How to Use It
April 08, 2024