Key Considerations to Look for When Designing a Burner Management System
A basic understanding of how to initially start to think extensively about your burner management system is necessary for ensuring that you are able to operate it safely and within compliance. When designing a burner management system (BMS), safety is the only one of many considerations. However, there are various other considerations that can be counted on when designing a burner management system.

Fired equipment is the core of petrochemical, oil and gas, manufacturing, refining, and many other industries. When designing a burner management system (BMS), safety is the only one of many considerations. Although there are many other considerations that are needed to be paid attention to.
The new designs and developments in BMS are focused on many considerations and provides increased safety and reliability. However, due to the outbreak of COVID-19, many governmental bodies around the globe implemented lockdowns to prevent the spread of the deadly coronavirus. This has led to a dramatic downsizing in business and industrial operations. According to Research Dive, the global burner management system market was estimated to garner US$ 5,600.4 million in 2020 but due to the COVID-19 pandemic, the global market is now predicted to reach up to 4,049.1 million.
Key Considerations When Designing BMS
A basic understanding of how to initially start to think extensively about your burner management system is necessary for ensuring that you are able to operate it safely and within compliance, and achieve a high level of reliability. Some of the key considerations when designing a burner management system include:
- Safety
After the safety codes and requirements are established, it is vital that those requirements are followed under all aspects of the burner management system. Safety rated and purpose-built controllers have in-built functionality that cannot be changed, which allows to comply with most of the safety related applications. General purpose programmable logic controllers (PLCs) with no in-built features can include; applying logic for input/output checking, hardwired master fuel trip circuits, proper operation sequence of BMS operations, and watchdog timing features that ensure the controllers are meeting the safety intent. In addition with the BMS controllers, it is critical that all field devices being used are safety rated and are installed with safety guidelines. Moreover, there are novel technologies to enhance the safety of your burner management system. For instance, some manufactures offer safety valves that beforehand perform partial stroke test, which ensures that the safety valve on the burner management system will close when it’s required.
- Compliance
National Fire Protection Association (NFPA), American Petroleum Institute (API), internal specifications, and insurance requirements are some of the considerations when designing a code compliant business management system. Code compliance addresses various aspects of the BMS from controller to the field devices. In order to easily obtain a code compliant BMS, follow the code that is required to adhere to. One area where BMS can be found out of compliance is where a customer is utilizing a general purpose PLC for the low level and high level stack trips of temperature. Per code, the low and high stack temperature loops must be controlled from an FM approved device.
- Reliability
A fired equipment gets the most attention it shuts down unexpectedly. It is necessary to understand the common causes of failure when designing a BMS. This helps your system to run reliably without any interrupted service. Various reliability concerns are raised up by the field instrumentation of a burner management system. Use of appropriate flame detectors for the service or application is one of the key component of reliability. The understanding of the combustion characteristics supports in the determination of the appropriate flame detector that would clearly identify all process combustion process conditions. This assists in mitigating any nuisance trips that can occur when the process conditions alter.
- Ease of Operation and Maintenance
Maintenance personnel are liable for the startup & shutdown of these burner management systems. Lights and interfaces should be intuitive to the operator concerned about the sequence & operation of the burner management system. In a fired equipment shuts down unexpectedly, it is vital that maintenance personnel act speedily to identify & analyze what went wrong and subsequently get the unit back-up and running. The BMS controller captures and displays whatever the critical limit lost while was shut down. Designing a burner management system that ensures a reliable & rapid way to identify shutdowns is needed to elevate the uptime of the fired equipment.
Conclusion
Considering these points when designing a burner management system can move you a step ahead of the curve. Although, it is necessary to make sure to periodically research the latest codes as NFPA and API codes change over time. Also keeping up with new developments & advancements in technology can increase the safety & reliability of your burner management system. This will allow you to build a BMS that is easier to operate & maintain in the future.
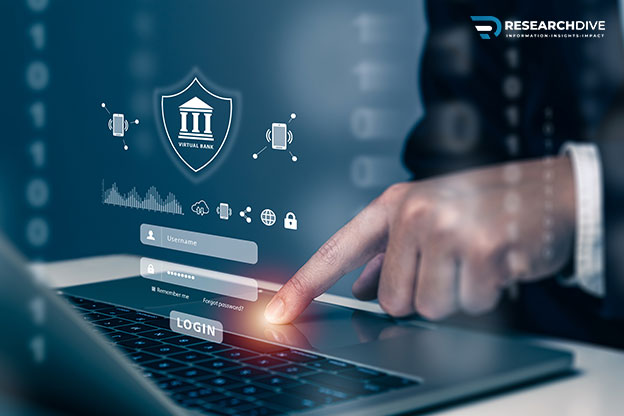
How is Cybersecurity Becoming a Vital Measure to Combat Emerging Threats in the Banking Sector Globally?
April 08, 2024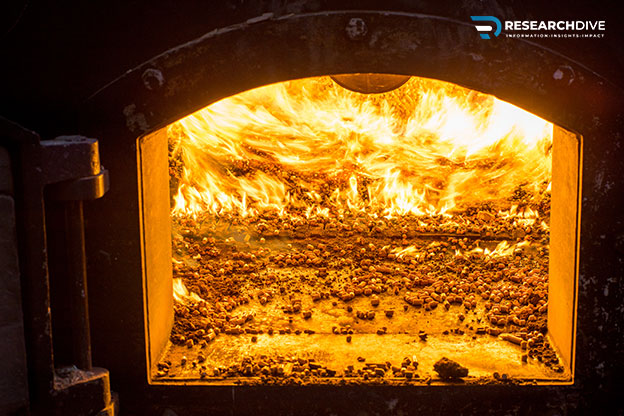
Wood Pellet Biomass Boilers: An Eco-Friendly Heating Solution
April 08, 2024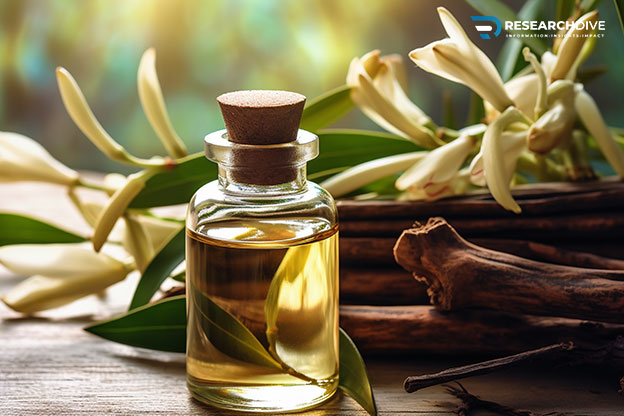
5 Ways Vanilla Oil Can Transform Your Life
April 08, 2024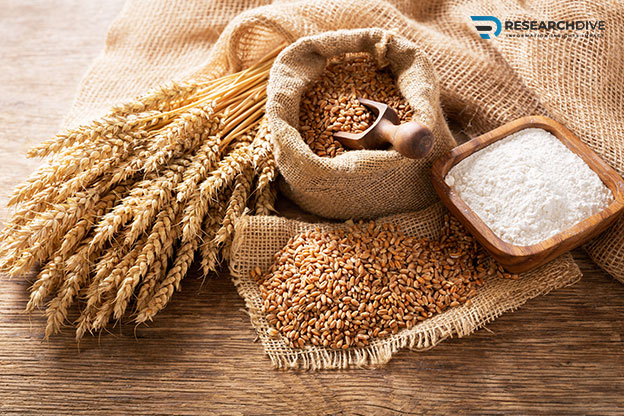
Discovering the Magic of Toasted Flour: Why & How to Use It
April 08, 2024