How Electronic Protection Device Coating Sector Safeguards the Gadgets
The electronic protection device coating sector has faced the effects of the Covid-19 pandemic. This sector utilizes various solutions to guard the devices from harmful pollutants. Various materials like acrylic, epoxy and urethane help in protecting the gadgets.

Gadgets – they have managed to install themselves in our lives and seem to have stuck on us like magnets. This dominant species emerging in today’s century has drastically changed our lives. Humans invented gadgets for ease of living and it’s up to mankind to care for these devices. A profound sector that has taken up the responsibility for protecting gadgets is the electronic protection device coating industry. This sector safeguards the crucial components of the devices by using various materials.
The electronic protection device coating sector helps in shielding the devices from contaminants that can shorten the device’s life. This sector uses materials like organic and inorganic compounds, polymers and metals for coating the devices. The usage of material depends on the function and application of the devices. Coatings are used for better functioning of electrical, magnetic, optic, mechanical and thermal factors. On the other hand, coatings also provide aid in circuit board manufacturing, protection and decoration of the devices.
Impact of Covid-19 on the Electronic Protection Device Coating Sector:
The Covid-19 pandemic has led to the shutdown of factories that manufactured electronic devices, thus, resulting in the downfall of the electronic protection device coating sector in the year 2020. However, this sector still holds a grip over healthcare and remote sensing industries during the pandemic. The electronic protection device coating sector continues to serve the healthcare and remote sensing industries as ample of gadgets are used there.
The post pandemic session will be a boon for the electronic protection device coating sector as the demand will enhance in the automotive industry. According to a report published by Research Dive, the electronic protection device coating sector will witness a rise in CAGR by 4.3 % by 2026.
Preferred Solutions by the Electronic Protection Coating Sector:
The electronic protection device coating sector provides a vast array of options for safeguarding the devices from contaminants. A few noteworthy solutions are mentioned below:
Acrylic:
This material is fungus proof and dries in 30 minutes at room temperature. Acrylic is feasible for rapid production of devices; however, it cannot survive temperatures above 125?C. This eliminates the possibility of using acrylic for excessive heat emitting devices.
Epoxy:
The coating strength of epoxy is the highest and has the potential to resist abrasions, vibrations, chemical incursions, and humidity. This material shrinks during polymerization process and possesses low stress resistance during extreme temperatures. Furthermore, it is difficult to repair and rework epoxy compound.
Silicone:
This material has the ability to tolerate temperature till 200?C, thus, it is used in automobile industry. Silicone can resist corrosion and humidity; however, it is powerless against abrasions and solvents.
Urethane:
This material supports Nano miniaturization by providing insulation to the electronic signals situated close to the printed circuit board (PCB). Urethane has longer dielectric functioning and resists solvents, humidity and moisture. However, urethane is difficult to remove and cannot be used in high temperature and vibration conditions.
Chemical Vapor Deposition (CVD) Derived Parylene:
This material provides continuous, consistent and pin-hole free conformal films. The gaseous Parylene can easily permeate through ceramic, resins, plastics, paper, metal, glass and ferrite. The CVD Parylene coating can blend in any geometrical shapes like crevices, corners, edges, and internal spaces. This durable micro-thin film has high dielectric strength and chemical inertness. The CVD Parylene is compatible with various devices; however, it is an expensive material.
Ultra Violet Coating:
This type of coating protects the devices from the harmful UV rays. The coating guarantees higher curing time when exposed to UV light. One of the UV lights called the UV Florescence light glows in the dark, thus, simplifying the verification and inspection of the material used.
Brush Coating:
This is a manual process which is used for small scale products. The accuracy, precision and consistency of the protective coating depend on the person’s skill and practice.
Dip Coating:
The printed circuit board (PCB) is dipped via machine, thus, coating the entire surface. This technique is unsuitable for components that lie in close proximity on the PCB because of low viscous flow of the coating.
Conformal Coating
These are thin polymeric films that protect the solder joints, leads of electronic components, and metallized areas on PCB from corrosion. The conformal coatings protect the devices from pollution, water, moisture, UV light, chemicals, and high temperature. The hydrophobic properties of the conformal coatings add on to its versatile nature. This type of coating is used in aerospace, automotive, consumer products, LED industries, marine, military, and energy sectors.
The Road Ahead:
The electronic protection device coating sector ensures the longevity of the devices, thus, making the devices durable, reliable and consumer friendly. The various methods, materials, and techniques used to safeguard the gadgets have enhanced the significance of electronic protection device coating sector.
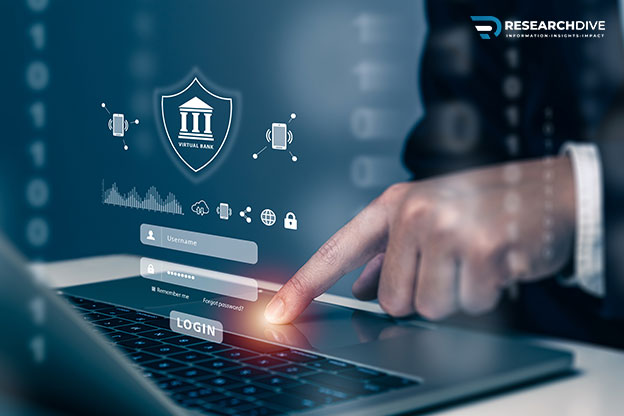
How is Cybersecurity Becoming a Vital Measure to Combat Emerging Threats in the Banking Sector Globally?
April 08, 2024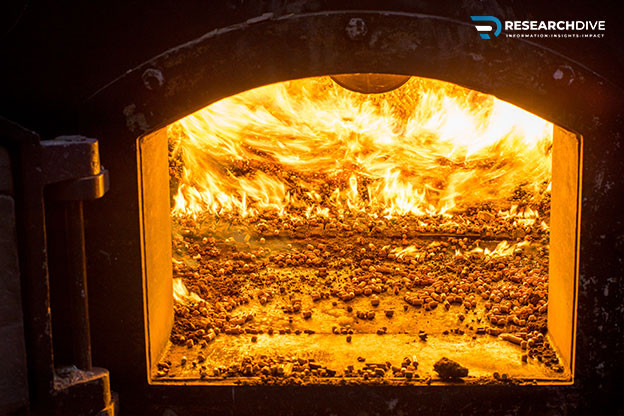
Wood Pellet Biomass Boilers: An Eco-Friendly Heating Solution
April 08, 2024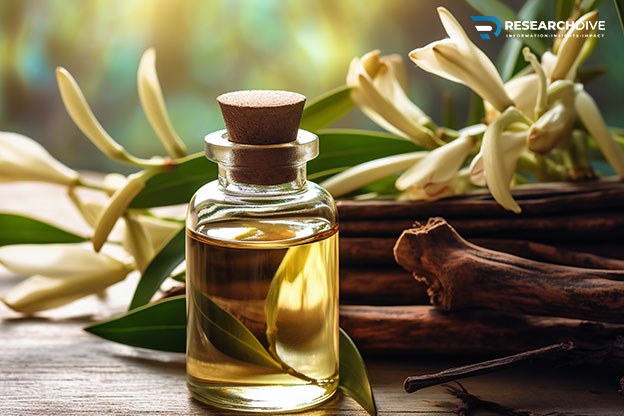
5 Ways Vanilla Oil Can Transform Your Life
April 08, 2024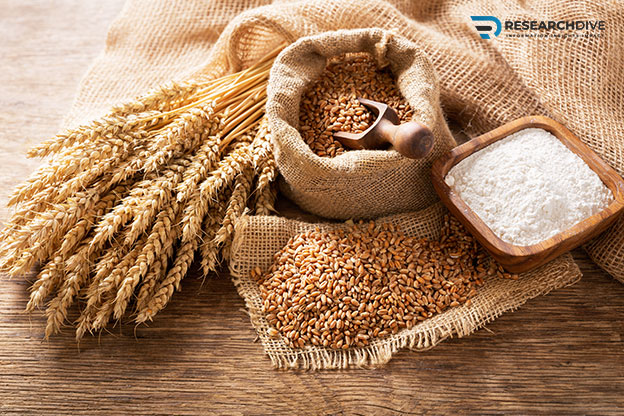
Discovering the Magic of Toasted Flour: Why & How to Use It
April 08, 2024