How Does Electronic Protection Device Coating Support Electronic Devices?
The electronic protection device coating industry plays a significant role in preserving the shelf life of electronic components and protecting them from harsh temperatures and environments. Despite facing adverse impacts from the outbreak of the Covid-19 pandemic, the sector is expected to revive its growth rate by 2023 due to the increasing usage of gadgets and other electronic items.

Leading our lives without electronic devices and gadgets is impossible since we’re so submerged by the ease and comfortability that they provide us. From smartphones, TV, laptops to refrigerators and vacuum cleaners, humans cannot survive a single day or perform to their optimum best without these gadgets. And in the modern era, almost everything works at a click of a button to help us work promptly. The power of gadgets is a blessing for us in every sense. And so, it is our responsibility to nurture this blessing and preserve electronic devices from environmental attacks like dust and moisture. The electronic protection device coating industry safeguards crucial devices by using several protective materials.
And as per a comprehensive report published by Research Dive, the global electronic protection device coating market is estimated to gather a revenue of $19,254.2 million and grow at a stable CAGR of 4.3% in 2019-2026 forecast timeframe. Considering this remarkable growth rate, it is evident that the industry is here to stay and bring in innovations to further uplift its protection methods and increase the gadgets’ shelf life.
However, this industry has also witnessed some major downfalls during the outbreak of the Covid-19 pandemic, just like any other sector. Let’s see the impact of the corona virus pandemic on the global electronic protection device coating market.
Covid-19 Impact on the Electronic Protection Device Coating Industry
The onset of the Covid-19 pandemic has had an adverse effect on the global electronic protection device coating market and has caused a shortage of workforce in the manufacturing units due to social distancing norms and travel restrictions imposed by governments all over the world. In addition, stringent lockdowns in countries also resulted in severe disruptions in supply chains and availability of raw materials, thus slowing down the production rate. Moreover, since the manufacturers in China had completely shut down their operations during the pandemic stress, the product availability in other countries also declined further since China is the main link of all electronic components. However, market analysts predict that the industry might revive its growth rate in the 2nd or 3rd quarter, i.e., 2023 due to the growing implementation of electronic protection device coating systems in the automotive sector and medical devices manufacturers.
Factors to Consider While Choosing the Right Electronic Protection Device Coating System
Since gadgets perform extremely complex tasks in automotive, IoT, medical, industrial applications, and consumer electronics, the demand for electronic protection device coating systems has increased exponentially. Here are a few factors you must consider while opting for any conformal coating:
- Corrosion protection
- Low moisture vapor transmission rate
- Low water absorption
- Low outgassing
- High insulation resistance
- Low dissipation factor
- High dielectric constant
Common Solutions Preferred by the Electronic Protection Device Coating Industry
The electronic protection device coating sector offers a wide array of preventive solutions to safeguard electronic devices and other gadgets. Some common solutions are as follows:
- Epoxy
Epoxy coatings have an epoxy resin and a polyamine hardener, and this mixture helps in the protection of electrical components from short circuits, dust, and moisture. Since epoxy resins have better thermal conductivity, they help in prolonging the service life of the components.
- Acrylic
Acrylic coatings provide elasticity to electric circuits along with excellent protection against fungus, moisture, and dust. This type of coating is highly preferred due to its ease of use, affordability, high abrasion resistance, and high dielectric strength.
- Silicone
Silicone conformal coatings protect printed circuit boards (PCBs) from harsh temperatures and other environmental conditions like chemicals, vibration, moisture, etc. Moreover, silicone coatings are highly water-resistant and flexible and so, have higher demand in PCB manufacturing sectors.
- Parylene
Parylene coatings are highly durable, conductive, flexible, and protect PCBs from several environmental threats like temperature, moisture, dust, mechanical forces, chemicals, and electric currents.
- Polyurethane
Polyurethanes are highly insulating, flexible, chemically resistant, and protect the electronic parts from oil, chemical corrosion, moisture, and static discharges.
Final Thought
The electronic protection device coating industry ensures the longevity of electronic components and makes them reliable, safe to use, and highly conductive. The coating solutions mentioned above are just a few of the many that are widely used in the industry to safeguard electronic gadgets and further enhance their service life.
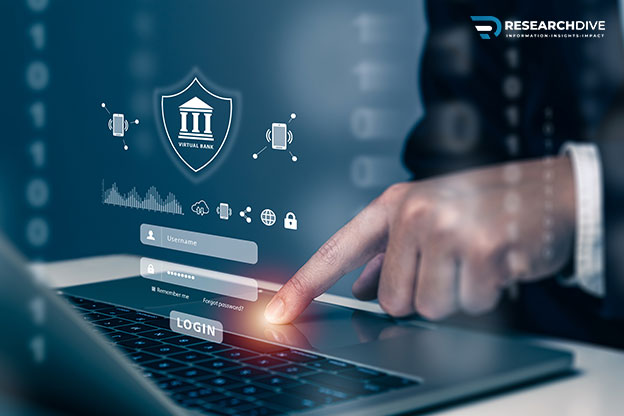
How is Cybersecurity Becoming a Vital Measure to Combat Emerging Threats in the Banking Sector Globally?
April 08, 2024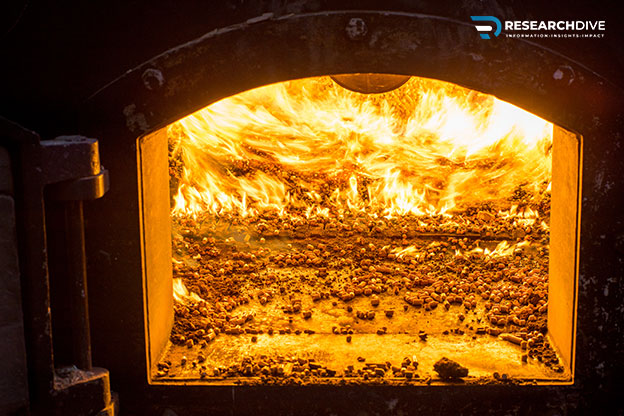
Wood Pellet Biomass Boilers: An Eco-Friendly Heating Solution
April 08, 2024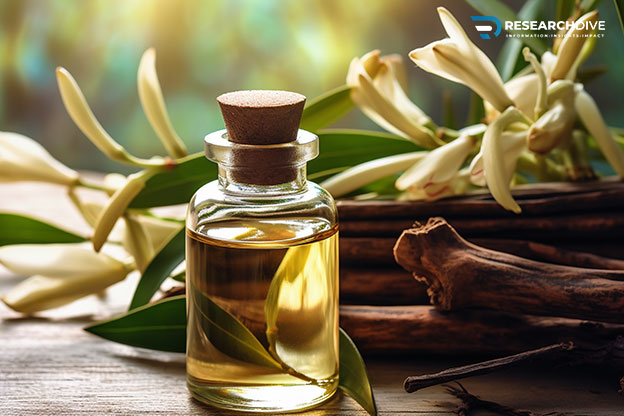
5 Ways Vanilla Oil Can Transform Your Life
April 08, 2024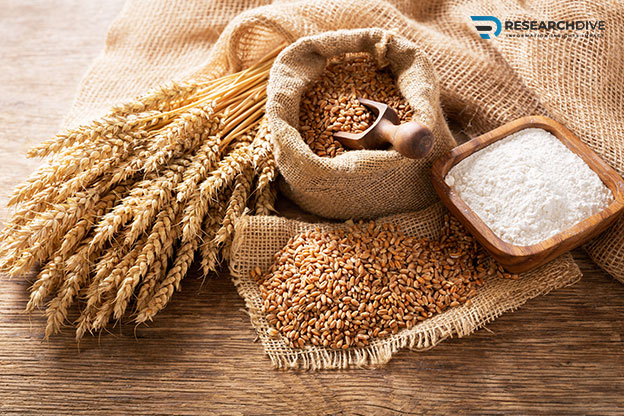
Discovering the Magic of Toasted Flour: Why & How to Use It
April 08, 2024