How a Post-COVID Supply Chain Could Take Shape in Asia, Exclusive of China?
The coronavirus outbreak has enforced border closure and lockdowns across the globe and instigated heavy disruptions to various business operations and consequently the growth trajectory of a number of countries in Asia. Hence, modern supply chains are facing unexpected stress and are pulling an increased level of scrutiny. It is now time to fundamentally rethink supply chains to make it more regional and modify it as a key business driver.

As the COVID-19 wreaked economic turmoil across the globe and the modern supply chains are facing unexpected & unwanted stress and are pulling an increased level of scrutiny. Border closure and lockdowns due to the coronavirus outbreak have instigated heavy disruptions to various business operations and consequently the growth trajectory of a number of countries in Asia.
Prior to the COVID-19 crisis, the US-China trade tensions had been rising for moths due to the mounting tariff war between Beijing and Washington, and a bigger populist streak was gushing through several other capital cities. Thus, the rise in protectionism, along with new financial barriers and concrete costs, fueled concerns and broader challenges for logistics networks operating on a worldwide level.
From Globalization to Regionalization
The logistics hubs will resurface at the regional level. To establish a flexible & adaptable supply chain and to exclude single-source dependencies, product integrators, component suppliers, and sub-system suppliers will source, accumulate, and deliver from their own yards. However, over several years, that change had been kicked off because of the rising Chinese labor costs. Low labor costs were once the major attraction for many companies towards Asia, but over the past few years, the labor cost variance has shrunk. The one thing that continues to hold the foreign attention is the whole supply chain network of sub-suppliers and suppliers located in the Chinese hubs.
Today, large number of electronic equipment manufacturers source around 40% of their parts from China, which also includes sub assembly. Given that there are exceedingly high number of parts required and each with different lead times, a return to regional supply chains can present a very complex challenge. However, this challenge might be valued or worth taking in the post-COVID world.
China’s Expense and Asia’s Gain
It is observed until now that companies in Asia have only focused on the economic returns & advantages of manufacturing in China. Lately, there has been a distinguished uptake in hostility towards the country unobstructed to the West alone. Some of the countries such as Japan have even started creating stimulus packages in order to lure their corporations far away from China. The major reason is that companies increasingly rely exclusively on China to deliver manufactured goods. In addition, the coronavirus outbreak has exposed off in stark terms, just like the blockages in a manufacturing hub can get the whole system down. Although the stimulus packages are envisioned for companies to return to their origin of country that is very unlikely as manufacturing costs in developed countries are incredibly higher. The more likely scenario is factories moving further southward with Indonesia, India, Thailand, and Vietnam being potential beneficiaries.
India: Back to Being the Exporting Powerhouse of Yore?
In particular, India is attempting to take full advantage of the opportunity. The sub-continental giant is apparently preparing a plot of land that is twice the size of Luxembourg for various companies seeking to move out of the most populous nation of the world and has even reached out to around 1000 American MNCs. A powerful lobby group functioning to enhance the trade, ‘The US-India Business Council’ has witnessed a sharp upturn in India’s interest to fascinate supply chain companies, and both at central and state government levels. Companies already existing in India may well try to upsurge the production there. However, investment decisions are infrequently made in haste and thus these strategies are still in the empirical phase. Moreover, the decision of India to pull out of the RCEP (Regional Comprehensive Economic Partnership), 7 years of negotiation notwithstanding, even didn’t help its case.
Two steps taken in the right direction to mitigate fears of investors could be larger regional integration mainly because the global trade follows ‘sell where you make’ ideal. Less policy flip-flops vis-à-vis the Foreign Direct Investment (FDI) would be the second step. Foreigners are somewhat hesitant to invest in India due to decades of protectionism. The responsibility lies on the nation to change that perception for the better could well bode the shift towards Asian manufacturing and where China may not be the watchword anymore.
The New 3Rs for Post-COVID Supply Chain
The unprecedented disruption from the current COVID-19 pandemic provides a remarkable opportunity for businesses, despite its negative consequences. Companies can now act by assessing impacts on business the near and long term. In a condition, where demand changes swiftly and contiguity is expected, the futuristic supply chain must not only continue to focus on quality, cost, and delivery, but also need to be considered with reconfiguration, responsiveness, and resilience in mind.
- Responsiveness
The systems respond to inputs from the outward environment. The supply chain system counts on inputs such as commodity prices, customer order volume, and freight rates to act. Consequently, businesses should raise the value of obtaining real-time updates on the above listed inputs by upgrading from the outdated systems that often consist of fax machines and phone calls.
- Reconfiguration
Differentiating one’s supply chain simple like building extra plants in other jurisdictions. Supply chain involves restoring and redesigning functions in the system to be more plug-and-play. For instance, in extreme events or the event of future pandemics, could certain business functions like finance and procurement their operations from other least or less affected locations? Thus, necessary changes should be made to enable that.
- Resilience
Be prepared and think bigger to build resilience from the ground, starting with structure of organization, business procedures, and performance metrics to future-proof for the upcoming disruptive event. Every business is different and there is no one-size-fits-all.
COVID-19 has exposed the weaknesses of a globalized manufacturing system. In order to respond to this, there is a need to fundamentally rethink supply chains. Goals for the medium term should be set to make supply chain more regional, thereby modifying the supply chain as a key business driver and most important factor for an agile business to succeed.
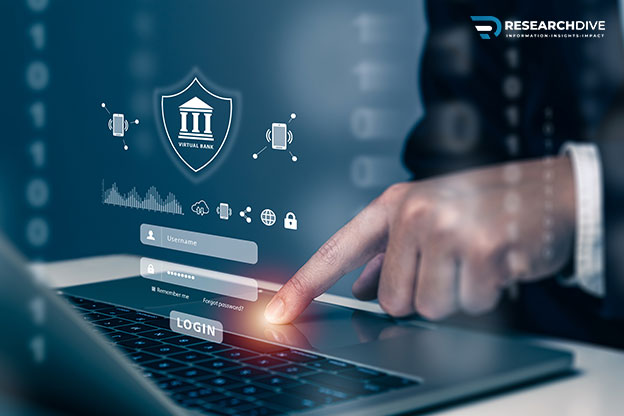
How is Cybersecurity Becoming a Vital Measure to Combat Emerging Threats in the Banking Sector Globally?
April 08, 2024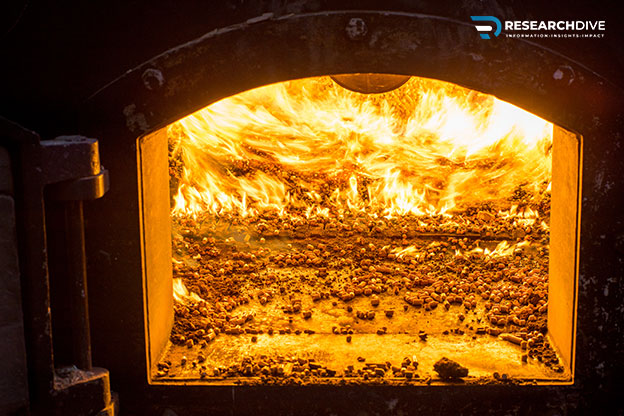
Wood Pellet Biomass Boilers: An Eco-Friendly Heating Solution
April 08, 2024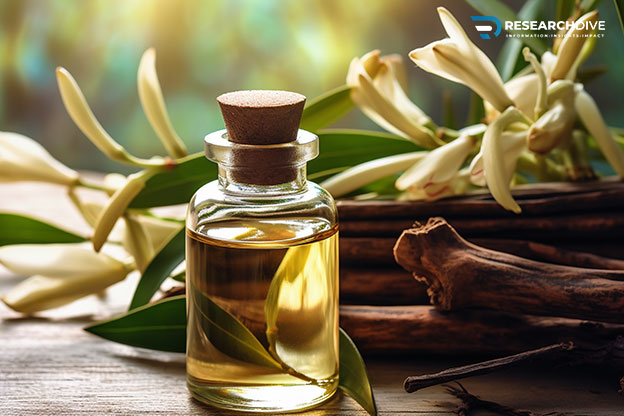
5 Ways Vanilla Oil Can Transform Your Life
April 08, 2024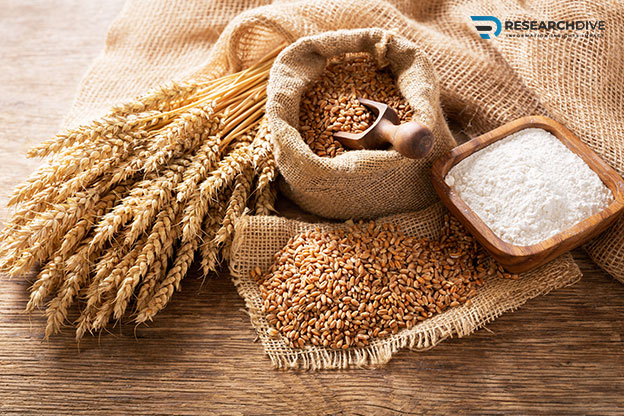
Discovering the Magic of Toasted Flour: Why & How to Use It
April 08, 2024